A robot from your printer
3D printing was a revolution, 4D printing allows you to print objects which take their final shape only after a trigger. In this project we want to go one step further: we want to be able to directly print self-actuating materials which can change shape continuously in a programmable matter.

Working principle
We do this by 3D printing bilayer strips of which the bottom layer contains a pattern of conductive silver ink which causes the layer to expand when heated by an electrical current. By adding a rim structure which is not affected by the heating we ensure a maximum effectiveness of operation (Figure 1 to 3). The printing is done with a Voxel 8 printer.
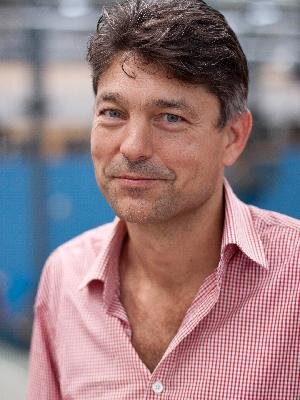
Kaspar Jansen
- +31 (0) 152786905
- k.m.b.jansen@tudelft.nl
-
Room B-3-170
Graduate students
- Mariska Maas
- Julius Hofman
Researchers
- Song-Chuang Zhao (Postdoc)
Partners
- TU Delft
- Leiden University (prof. Martin van Hecke)
Demonstrator project
The actuation is reversible and when the power is switched of the actuator returns to its starting position. Exploring this idea allowed us to design 3D printed objects which can reversibly change shape. In the current project we chose to design a self-propelling object which can move forward by a series of controlled repetitive movements of its actuators.
New findings: reversible large deformations by controlled ratcheting
As a next step we integrated also heating elements on the rim structure. When the rim is cold the neutral plane for bending is above the inner heater plane such that heating of that layer will cause the actuator to go upwards. However, by switching the rim heating on the material softens and the neutral line shifts to below the printed heater lines such that the actuator now bends downwards upon heating!
In addition, in our paper we show that by sequentially heating the inner and rim heaters and each time relaxing part of the stresses we can create a ratcheting behaviour which cycle-wise increases the bending curvature to 15 m-1 after 8 cycles. Moreover, we show that this behaviour is reversible (see Figure 6).
Conclusion and challenge
In this project we showed that it is possible to 3D print actuated objects and demonstrated this with a self-propelling turtle. The movement is, however slow: the turtle in Movie1 actually takes about 7 minutes to advance 3 millimetres. The printing itself is straight forward, so:
We challenge other researchers to beat our current record of 0.4 mm/min forward speed.