Tree composites
Research Themes: Energy, Structural Engineering
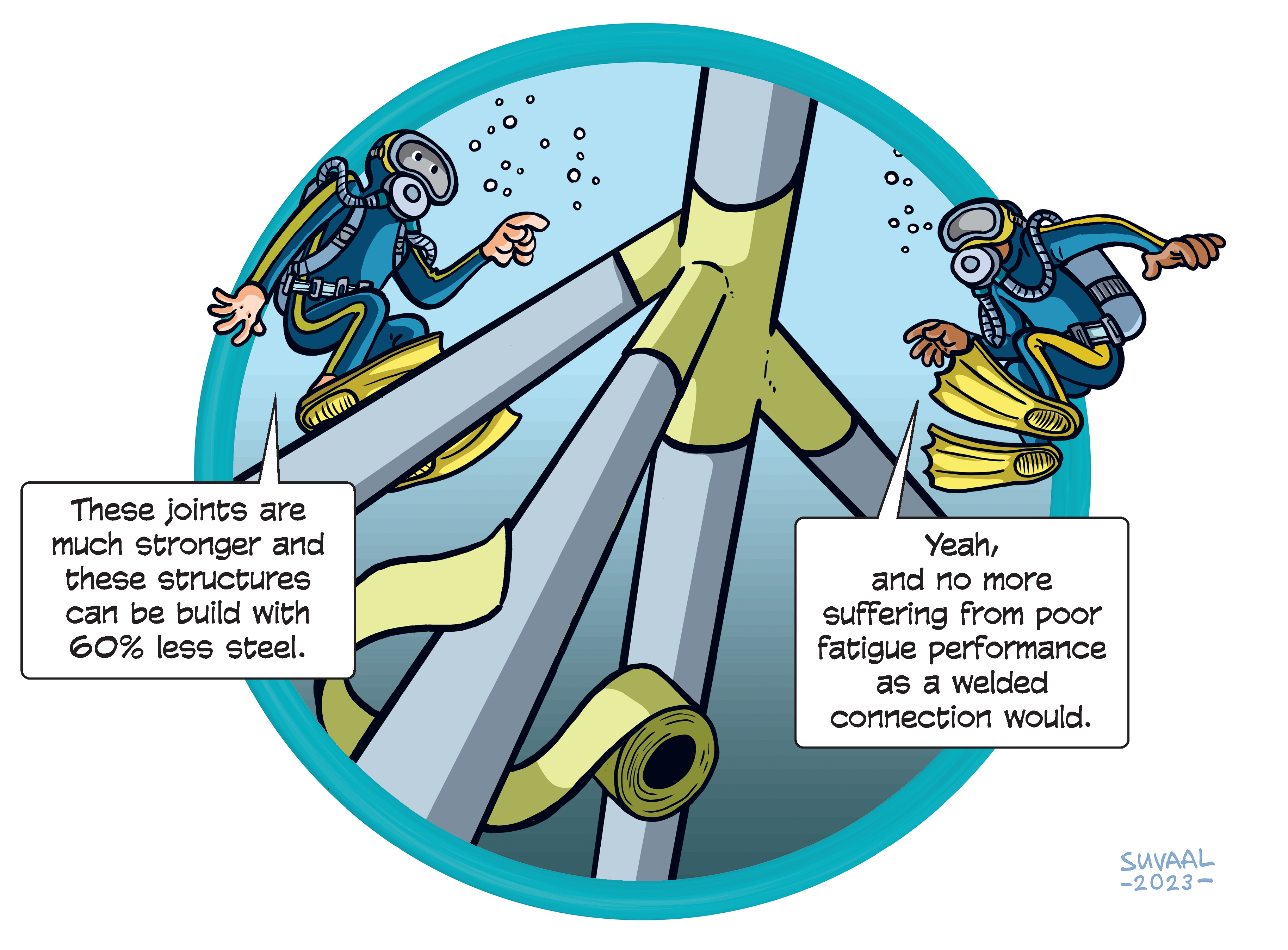

Summary of the project
Composite joints replace traditional weld in multi-membered structures such as a Jacket foundation for offshore wind. It is a gamechanger in construction as it transfers loads utilizing composite material placed strategically at location to create the optimum load transfer in a joint. This joint is thereby used the best of two worlds: Steel for its excellent stiffness and composite for its excellent fatigue resistance. When applied in heavy loaded offshore structures it reduces the amount of steel in a structure up to 60%. The biggest challenge for this technology is the acceptance of an innovation by and in the risk-averse market of Offshore wind. That is why we work closely with the supply chain and project developers.
What's next?
Since 2017 over 150 joints and 1000 material specimens have been tested and in 2023 full scale joints where tested and confirmed the maximum and fatigue capacities are in line with prediction models. Next steps are to finalize the qualification of the technology in 2024 and the focus lies on industrializing the production method to accommodate the volumes of offshore wind and introduction to the market by Pilots and scaled introduction of the technology.
Contribution to the Energy transition:
We propose a solution that increases the manufacturing capacities of existing yards by a factor 2 that supply structures such as Jackets and floater for offshore wind. At the same time we realize offshore wind foundations with up to 60% less materials, that generate 40% less CO2 and that have a superior lifetime of 5 to 10 times compared to current state-of-the-art welded offshore wind foundations. This will strengthen the supply chain in their challenge to increase their capacities and accelerate the deployment of offshore wind.
Dr.ir. Maxim Segeren
CEO
Dr.ir. Marko Pavlovic
Inventor
Additional information
- Links