Fatigue Behaviour of GFRP Bridge Decks
Project description
The research project focuses on the application of Glass Fiber-polymer Composite (a.k.a. GFRP) in bridge construction, an innovative material lauded for its excellent fatigue and corrosion resistance, and lightweight nature. The project involves experimental and numerical analysis of Composite bridge decks to understand their performance at ultimate loads and fatigue life, with a particular emphasis on the fatigue response, stiffness, and failure mechanisms of these structures.
By exploring the properties of GFRP in bridge decks, the project aims to deefine basis for the design and code verifications and allow for reliable, economical and sustainable design and implementation of such structures. This effort can lead to more optimized and sustainable civil engineering practices, especially in bridge renovation and construction. Moreover, the research is timely, aligning with the increasing adoption of GFRP in civil engineering in various applications and the necessity to fill knowledge gaps for broader acceptance.
Collaborating with Rijkswaterstaat (RWS) and industry leaders, the project not only contributes to the scientific community but also addresses public safety concerns and the sustainable optimization of civil infrastructures, such as pedestrian and highway bridges. The research's outcomes could play a pivotal role in the advancement and approval of GFRP in civil engineering.
TU Delft investigators: Dr. Marko Pavlovic, Dr. Olena Karpenko, ir. Tjeu Peeters
Experimental and analytical evaluation
The research involves an experimental campaign on scaled composite bridge segments, designed to emulate actual road bridges while allowing controlled failure within laboratory constraints. These tests are carried out at the Stevin Laboratory II (TU Delft), where a custom steel frame is engineered to support the specimens during monotonic and cyclic loading three-point bending test.
To capture a full spectrum of data, the experimental setup integrates multiple measurement systems. 3D Digital Image Correlation (DIC) systems, fibre optic strain measurement (FOSM), and linear displacement transducers work in concert to record displacements, deformations, stresses, and failure points.
Finite Element Analysis (FEA) complements the physical tests by simulating the bridge deck under various load conditions to predict maximum failure loads, displacements and dominant failure modes. In light of the large dimensions of the test specimens and the complex behavior of sandwich panel structures, FEA is indispensable. It not only provides a priori estimates of the experimental setup requirements, failure modes, and machine capacity but also reveals how initial imperfections might alter failure patterns.
Crucially, FEA offers invaluable foresight into the real-world performance of these decks, presenting a cost-effective supplement to the experimental procedures. By establishing predictive numerical models, the study gains deeper insights into the structural integrity of GFRP bridge decks, enhancing both the design process and material utilization in actual bridge construction.
Three-point bending experiments and numerical investigation at TU Delft
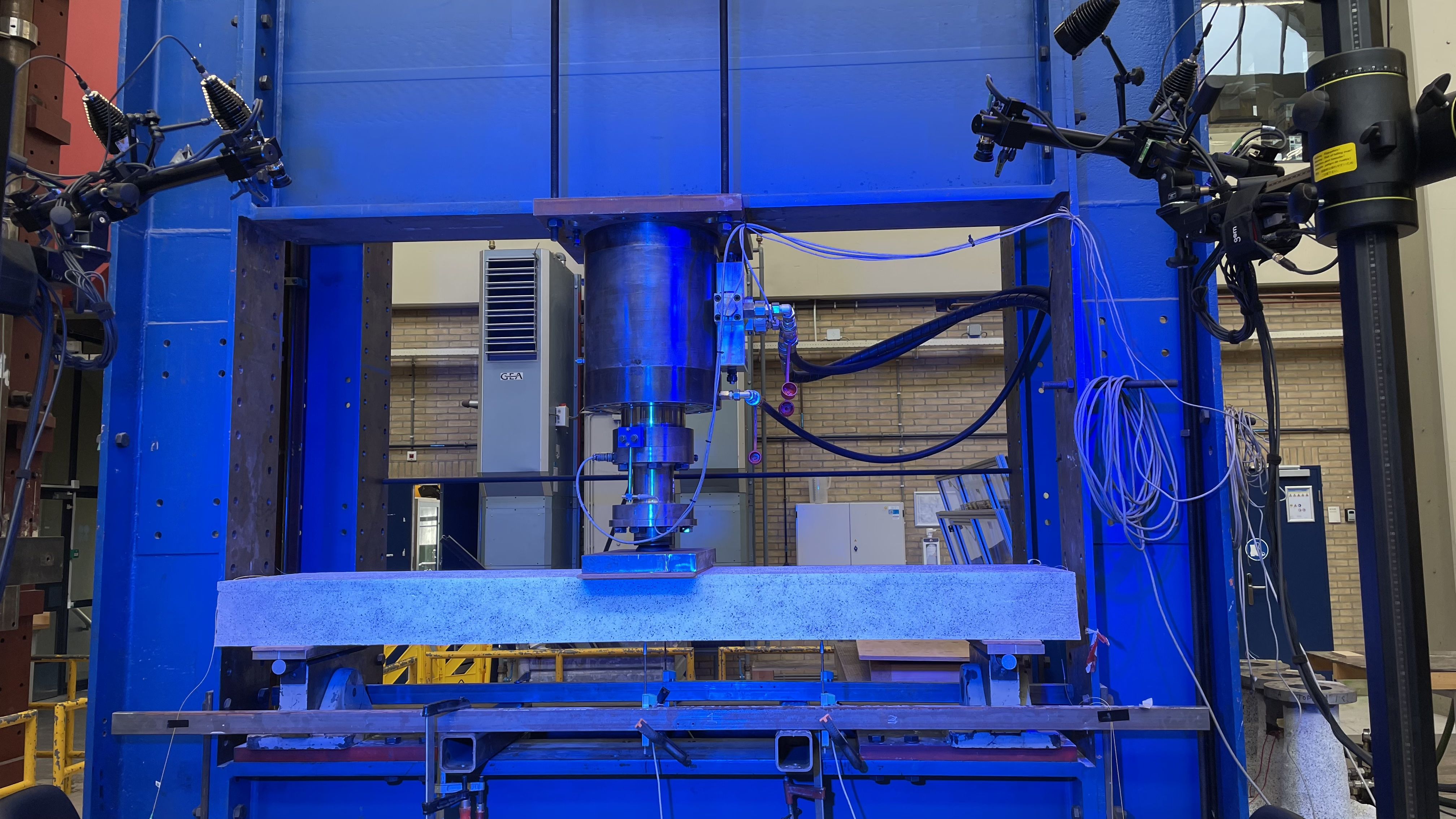
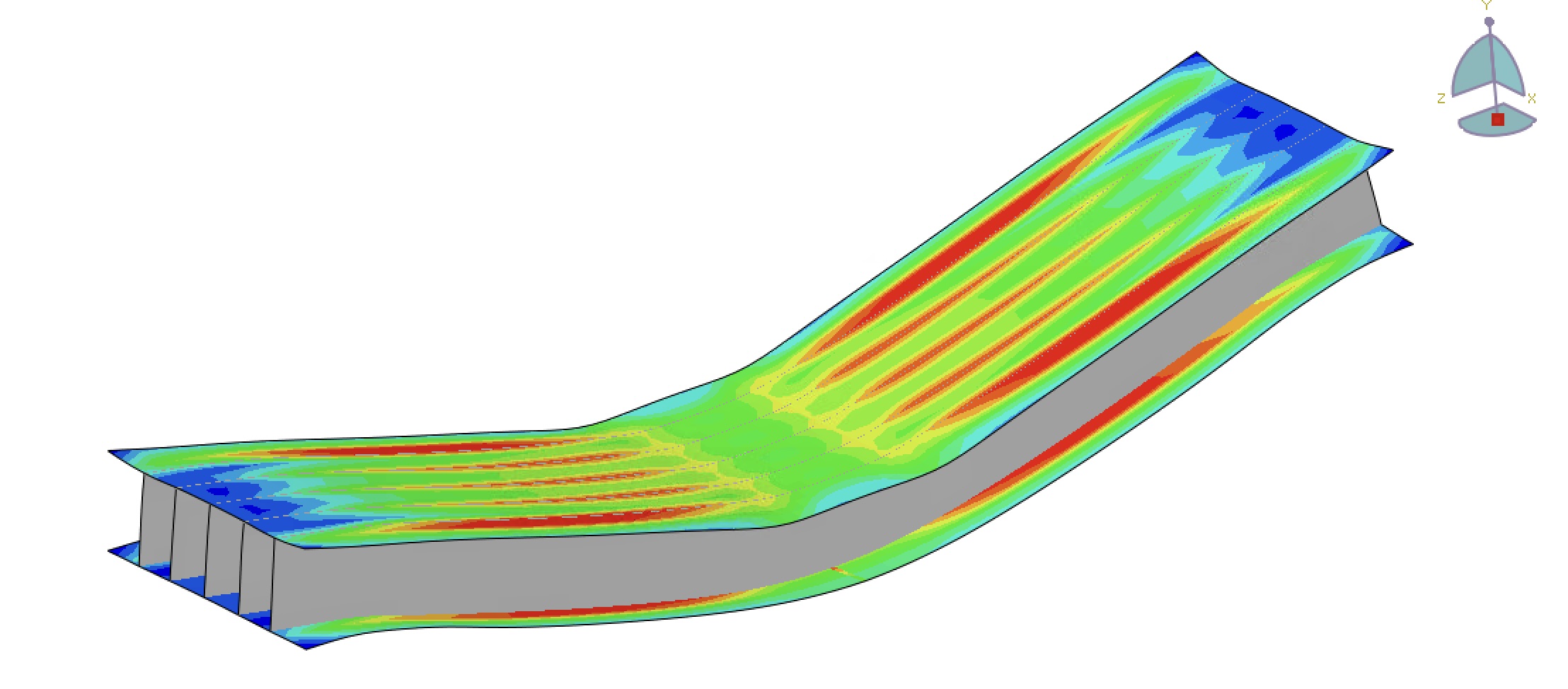