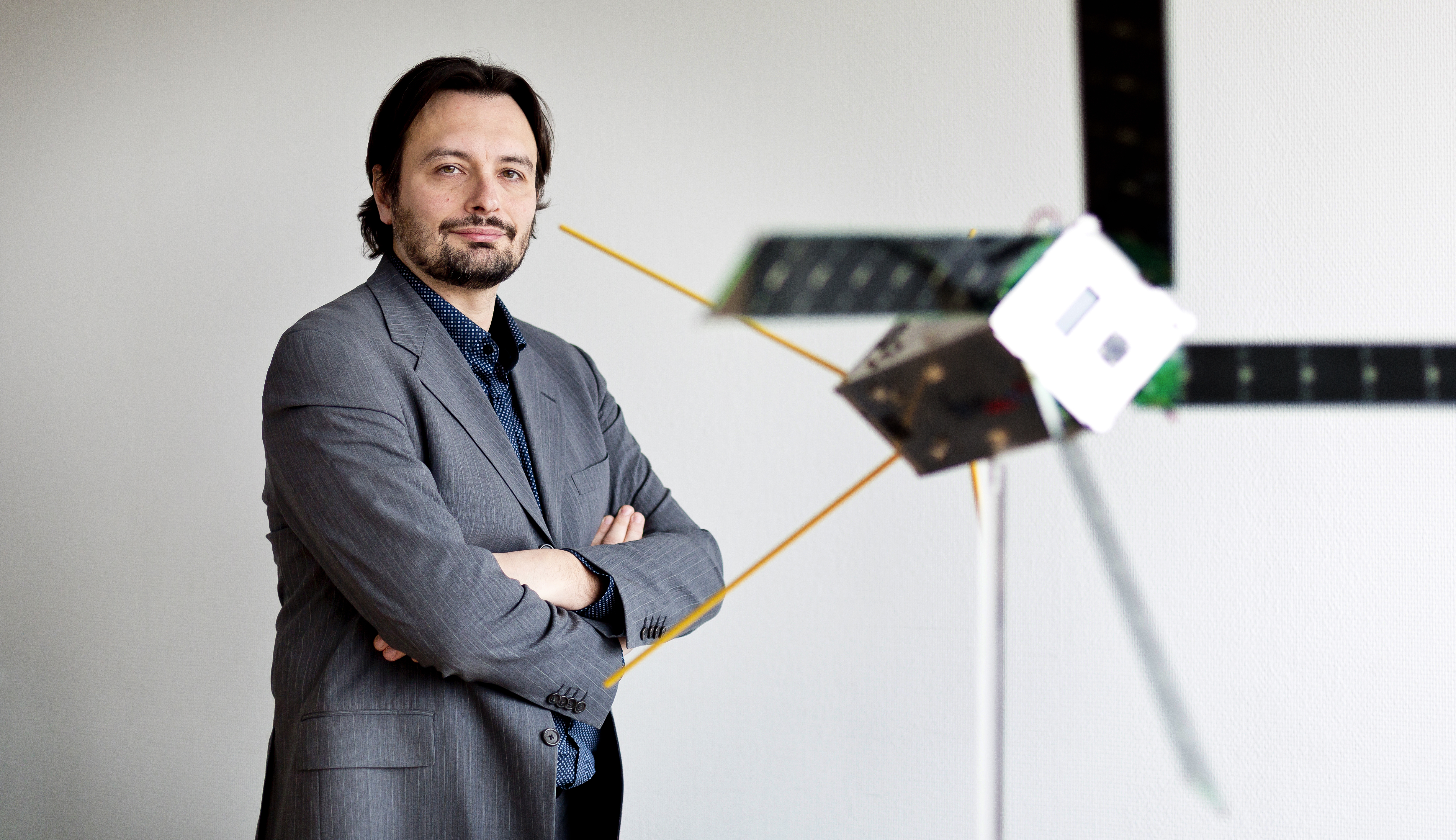
With the trend towards miniaturized satellites, the search is on for small-scale propulsion methods. The work of Dr Angelo Cervone in the department of Space Engineering (SpE) focusses on MEMS-based propulsion systems. “Small satellites today have very limited propulsion capabilities, meaning they cannot change orbit or perform complex manoeuvres. So the development of new micro-propulsion systems is already an achievement in itself,” he says. “It also opens up the opportunity of employing constellations of satellites flying in formation.”
Universities have long been leading the way in the development of small satellites. What started off as an educational tool to teach students how to build and launch satellites, has since gone mainstream. “Nano-satellites are no longer used for research and education only. A lot of companies are launching small satellites for imaging purposes and other commercial applications,” says Dr Angelo Cervone. In February 2017, a record-breaking 101 nanosatellites were launched aboard a single rocket from the Sriharikota space centre in India. These included 88 CubeSats from the US Earth-imaging company Planet Labs Inc, founded by a team of ex-NASA scientists. “Their goal is to image each point of the Earth’s surface every day, like a kind of Google Earth that is updated daily.”
None of these 101 CubeSats had propulsion, however. A propulsion system would allow such nano-satellites to correct their orbit or maintain their altitude, meaning they can achieve a much longer operating time in space. “At very low altitudes, in the order of 300 to 350 kilometres or less, there is still some air which generates a drag force and slows down the satellites, so they tend to fall into the atmosphere after a few months or even days.” Propulsion is also a key enabling factor for missions based on constellations of satellites flying in formation. “Satellites flying in formation must keep very precise relative positions. This is very hard to achieve without propulsion.” Sending a swarm of small satellites into space is a long-term goal of the SpE department: in the OLFAR mission, satellites will orbit the Moon and jointly form a virtual telescope, to study the dark ages of the universe.
Cervone has been working on space propulsion since his MSc and PhD research at the University of Pisa, Italy. After two years of post-doctoral research at the University of Osaka, Japan, he joined TU Delft in 2012. Here he focused his research on the development of propulsion systems suitable for the very small satellites the university is working on. That is not simply a matter of decreasing the size of existing larger systems. “Not everything scales linearly with size. Different performance factors scale in different ways with the design parameters, some of them linearly, others in a cubic or quadratic fashion. For example, reducing the size by a factor 10 will reduce the thrust by a factor 100, but also increases the chance of energy losses by a factor 10.”
Resistojets
While micro-propulsion is a fast-growing field, Cervone discovered that research into the thrust range of 1-10 millinewton (mN) is still a mostly uncharted territory for CubeSat-sized systems – a thrust range that would be very useful for CubeSats that have to change orbit or rotate rapidly. “Of course there are options that can provide higher thrust, but for a satellite the size of a CubeSat that would be a bit like putting an aircraft engine on a car: it’s too big for its size, causing the satellite to become uncontrollable.” This 1-10 mN range can be achieved by using resistojets, the particular propulsion option at which Cervone is currently working. “As far as we know, they are the only way to get to this thrust level with a still acceptable performance in terms of propellant and power consumption. Resistojets are not very efficient for larger satellites, so in spite of their apparent simplicity the research on them has not yet reached sufficient maturity. Looking at our requirements, however, they are the best option.”
In a resistojet, the propellant is heated via an electrical resistance and then expelled through a nozzle. “We use energy from the satellite’s solar panels to drive current through the resistor. This heats up the system, providing thermal energy which in turn heats the propellant,” explains Cervone. “We are looking into water as propellant, because it is ‘green’, safe, easy to use and, surprisingly, also offers an excellent performance. In a paper recently published in the ASME Journal of Heat Transfer we have demonstrated that, among all fluids storable as liquids at nearly-ambient conditions, water is the best one in terms of volumetric propellant consumption and the second best in terms of mass consumption.”
But before they got to that point, they had to create their own research instruments and facilities. “The first task of our team was to design an instrument to measure the thrust with sufficient accuracy. Consider that 1 mN is the weight force of a 0.1 grams of mass. That is approximately the same force you feel when you put a bird’s feather on your finger: practically nothing.” What the team came up with is a system based on a pendulum. “We put our propulsion system on the pendulum and then fire the thruster. That will make the pendulum oscillate a little, and we can measure the oscillation amplitude and relate it to the force.”
An important development will be a vacuum chamber to test their systems under conditions comparable to those in space. “With such very small systems there is a lot of uncertainty when you don’t test them in vacuum, because normal atmospheric pressure can be more than enough to counteract the thrust. To understand what really happens in space we need a vacuum chamber.” For now they are using a vacuum oven where a moderate level of vacuum can be reached, albeit still far from the actual conditions in space. “We are also considering the option to use vacuum chambers already existing elsewhere, such as those at ESA-ESTEC, but we would obviously get only limited time slots there. We really need our own chamber to test what we want, whenever we need it.”
Manufacturing
Manufacturing micro-propulsion systems is another challenge, as the complete system containing the heating system, propellant channel, nozzle and even a water tank can be as small as a sugar cube. “The components of our systems have sizes ranging from a few millimetres to much smaller, sometimes as small as a human hair, and heavy integration between fluidic, electronic and structural components is required,” says Cervone. That is why the team turned to MEMS fabrication technology (MicroElectroMechanical Systems), for which they collaborate with the university’s Else Kooi micro manufacturing lab. Using MEMS offers great opportunities for further integration. “Apart from the heaters, nozzle and channels, MEMS also allows us to integrate electronics like sensors and the control system for the thruster,” says Cervone. “We are also thinking of adding a MEMS valve, a moving element that opens and closes the channel, which is now still a separate component outside the chip. The valves we are currently using measure a few centimetres, so they definitely require further miniaturization.”
Micro dimensions also make high demands on the materials used. For example, too large a difference in the rates of expansion and contraction as functions of temperature is not acceptable, as even small relative changes in dimensions can have high impact. “MEMS are mainly made with silicon, a material with relatively high thermal conductivity. It dissipates heat very fast to the external environment. For propulsion that is a problem, since we need to transfer as much thermal energy as possible to the propellant without dissipating it. You want to supply the heat to the propellant, not to space”, says Cervone. “One solution is to better isolate the system by covering it with special paintings or materials.”
In the long term, they are also looking at 3D printing. “With 3D printing you can design and manufacture any kind of complex shape. Unlike traditional manufacturing, which works by joining parts or removing material from them, a 3D printer makes your design in one piece without any seams or joints. The technology is not yet mature enough at the micrometre scale we need, but is progressing very fast and I expect it to advance to that level in a few years.”
Satellite-on-a-chip
Further miniaturisation can ultimately lead to satellite-on-a-chip concepts. “Chip-sized satellites could be disruptive in space missions. Imagine you can send such small chips into space, and do almost everything with them that we are doing now with larger satellites. Ideas that still sound like science-fiction today could then become reality, such as the Breakthrough StarShot project supported by Stephen Hawking and Mark Zuckerberg that aims to send chip-sized satellites to Proxima Centauri, the star nearest to our solar system. We are not quite there yet, though, we still need a bit more research.” Watch this space.